PVTIME – China’s installed solar PV capacity has been growing over the past decade. And now the global PV industry is led by Chinese solar manufacturers. In 2023, global renewable energy capacity additions will reach a significant milestone, increasing by almost 50% to nearly 510GW. This growth rate is the fastest in the last two decades and, as the IEA notes, was driven by China. China’s acceleration was exceptional, with 216.88GW of new solar capacity added in 2023, more than the entire world added in 2022.
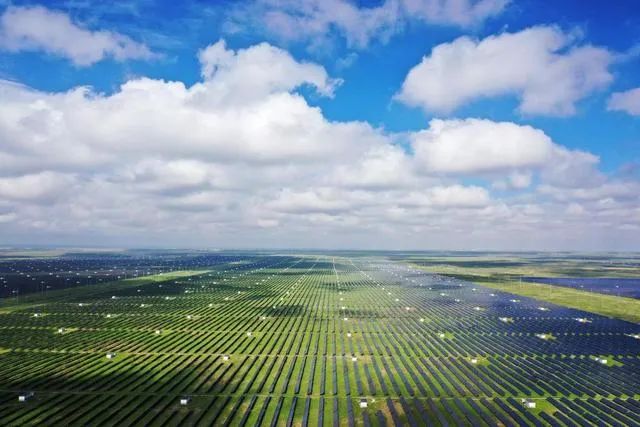
The development and deployment of solar PV is critical in 2024. The reform of the solar PV market, mainly driven by extremely low prices and overcapacity of raw materials, had created challenges for all manufacturers in the supply chain. Many solar-related manufacturers are suffering from the unstable market, with the exception of mounting and tracking system providers.
Nextracker, the leading solar tracker provider, achieved revenues of $1.9 billion in FY2023, an increase of 133%, and net profit of $121.3 million, up 243% year-on-year.
The global market share of tracking systems is at a relatively high level of 47%, and even reaches 80% in some preferred countries and regions. However, in China, the market share of tracking system remains at the level of 7%~8%, which is much lower than the usage rate of fixed mount.
Is tracking system better than fixed structure?
Photovoltaic mounting system is a special support designed to place, install and fix solar panels in the solar power generation system.
As the skeleton of the PV power plant, the mounting system has an important influence on the lifetime of the PV power generation system and the power generation efficiency. The design of the bracket must be based on the local geographical location, environment, climate and other conditions, the bracket will be maintained at an angle to maintain a maximum area for receiving sunlight radiation. its location is fixed and will not be adjusted frequently. The stability of the structure is a key factor in determining the lifespan of the PV power plant, as well as the overall income of the plant. A well-designed mounting system with appropriate angles will not only extend the overall life of the system and increase power generation efficiency, but will also significantly reduce future maintenance costs.
Photovoltaic power generation systems must operate smoothly for 25 years under various adverse conditions such as sandstorms, snowstorms and earthquakes. In the cost composition of the whole PV power generation system, the cost of the tracking system accounts for about 16.3% of the total cost of the system.
The power generation of the solar plant with tracking system could be increased by 5% to 35% compared to the plant with fixed bracket in the same area. Meanwhile, the cost of the whole system with tracking devices will increase by about 0.2 yuan per watt, involving costs on the bracket, area, electrical control and drive system, and maintenance, compared with fixed mounts. In addition, the area required for the tracking system is greatly affected by latitude, especially for the inclined single-axis and dual-axis tracking systems. In a 50 degree latitude location, the area for a solar system with a tracking system is almost 8 times larger than in an 18 degree latitude location, while the area for a fixed mount is less than 5 times larger. Therefore, the advantage of the tracking bracket cannot be set if it is in the place with high land price.
As mentioned above, the tracking bracket is higher in height, more difficult to clean and maintain compared to the fixed ones. And the increased cost on the self-consumption of electricity of tracking system as well as relatively higher failure rate, make it not preferable as fixed ones.
In the Chinese solar market, the understanding of tracking bracket was insufficient in the early photovoltaic power plant installation. The fixed mount was chosen for its low cost and low technology, while the early tracking mount has low technological maturity, insufficient stability and produces some quality problems, which affects investors’ confidence.
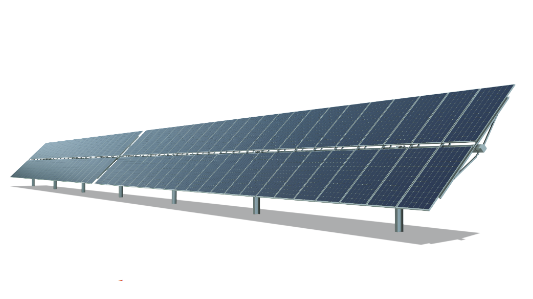
But the situation has changed.
Taking a 30MW N40° PV project as an example, the maintenance cost of a fixed bracket solar power plant is assumed to be 4 million yuan per year, and the maintenance cost of a similar tracking solar power plant is assumed to be 4.8 million yuan per year. The difference between the two is not huge. And it is estimated that the ROI of a solar power plant in the same location with a single-axis tracking system that can adjust the angle of the solar modules within 30° can be dramatically improved.
The future market for trackers in China is expected to be optimistic, with a market size of 65.1 billion yuan in 2025. the market for trackers will grow along with the installed capacity of solar power plants. A broad market for trackers will be developed at high speed as the solar market expands and the construction of solar power plants accelerates. Meanwhile, the tracking system is an energy-saving system with relatively stable electricity demand. The use of tracking system can bring higher IRR for solar power plant when the increased operation and maintenance cost of tracking bracket is 0.03 yuan/w, and the calculated gain in power generation of tracking bracket reaches more than 7%.
There is huge scope for solar trackers to reduce costs. In recent years, the profitability of solar tracking system was not so high due to the increasing price of steel and high shipping cost. And the whole solar industry in China put their attention on technology innovation mainly on silicon wafer, solar cell and modules, not so much on tracking system, which actually requires upgrading and improvement for lower cost. the bracket product innovation and upgrading, also the key to PV power plant cost reduction and efficiency.
We know that the cost of raw material could reach 70% of the total cost of solar tracker, of which more than 60% is steel. The raw material cost of fixed mounting and solar tracker is 72.58% and 65.29% respectively. The cost of driving part, such as electric control box and rotational deceleration device, accounts for 12.05% and 9.89% of the total cost, respectively. Therefore, the fluctuation of steel price has an important impact on the profitability of PV supporting systems.
Since 2023, steel prices have shown a decline, which provides favourable conditions for improving the profitability of PV mounting and tracking.
Taking Arctech, a leading Chinese smart tracking and mounting system provider, as an example, in the first three quarters of 2023, it achieved operating revenue of 3.393 billion yuan, an increase of 50.22% year on year, and net profit of 157 million yuan, an increase of up to 1,353.77% year on year. Similarly, Clenergy Technology, a Chinese mounting solution provider, achieved growth in both operating income and net profit, up 26.02% and 112.20% respectively year on year.
In addition to the decline in raw material prices, the improvement in the PV mounting industry’s profitability is also due to the continued growth in market demand. With the deepening global attention on carbon emission reduction and clean energy, more than 100 countries have increased the construction of photovoltaic power plans. China as one of the world’s largest photovoltaic market, its photovoltaic installed capacity continues to grow, providing a broad market for photovoltaic bracket. It is expected that in the next few years, with the further expansion of the global installed capacity of photovoltaic, the market size of the photovoltaic bracket industry will continue to expand.
Some institutions predict that in the next few years, the market size of tracking in China is estimated to reach more than 40%. Overall, tracking and mounting by increasing the solar power generation rate, can become a new point for the photovoltaic industry to reduce cost and increase efficiency.
It is worth noting that despite the bright prospects of the tracking system market, there are still some challenges to overcome. These include how to improve product reliability and reduce operation and maintenance costs, and how to further reduce costs to meet the needs of more customers, etc. These issues need to be addressed through joint efforts within and outside the industry.
PV tracking requires more design and development capability and experience from manufacturers, and the tracking industry is a technology-intensive industry with high technical barriers.
The main barriers are: system design, algorithm design and AI application. The bracket is a highly customised product, and the tracking bracket needs to consider both efficiency and stability. In addition to the need to consider static force stability, as in the case of fixed brackets, it is also necessary to consider rotational balance, vibration damping and other dynamic balance.
At the same time, the amount of steel should be minimised to reduce costs, which requires multi-disciplinary knowledge such as fluid mechanics, material science, mechanical design, intelligent control, power engineering, mathematical algorithms, simulation design, etc., and requires a high level of team ability and experience.
In addition to the inherent mechanical design, machining and outsourced galvanising of the fixed bracket, the tracking bracket also requires additional electronic control and drive design depending on the specific project and geographical conditions for the appropriate assembly.
The mechanical, electronic control and drive design should not only meet the basic requirements for stable operation, but should also match each other to achieve a better synergistic tracking effect. Therefore, the tracking mount has higher design requirements than the fixed mount.
Algorithm design and AI application: subject to the influence of geographical location and environment, there is a big difference. Suppliers must first complete the basic design of tracking algorithms according to the geographical location of the project (longitude, latitude and altitude) and the geographical environment (flatness, obstruction or no obstruction, etc.).
It must then take into account one-sided and two-sided situations, shading, land costs, etc., in order to obtain the optimal layout and optimise the tracking algorithm. The complexity of the scenario, such as cloudy days and other weather that shades the sun, makes it clear that the component cannot absorb the maximum amount of light by relying only on time control to track the sun.
Most Chinese PV manufacturers tend to adopt an integrated business model, including R&D and design and manufacturing, which brings more quality control and cost advantages. Manufacturing products in China is conducive to the company’s personal control of product production, shortening the product production cycle, ensuring product quality and delivery time, and controlling production costs. Overall, under the integrated production mode, China-based companies have stronger delivery capability and more competitive advantages in continuous technology iteration and low-cost product production. They have also begun to catch up with the top tracking system providers in terms of design, channels and other aspects.
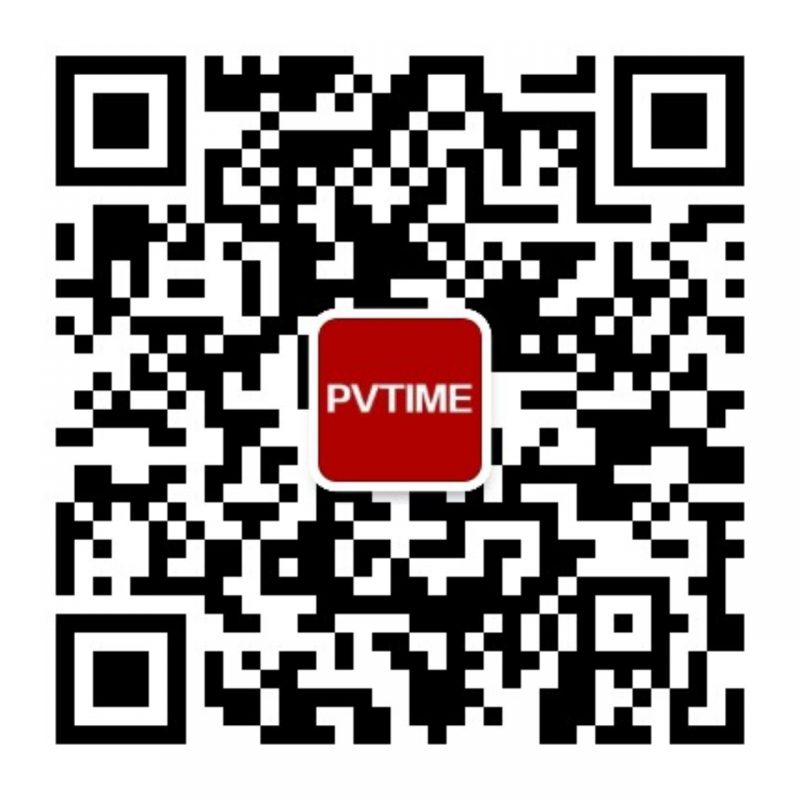
Scan the QR code to follow PVTIME official account on Wechat for latest news on PV+ES